月刊ゴルフ用品界2018年1月号に掲載された「現場放浪記 第8回」をWeb用にアップしたものです。なお、記事内容は本誌掲載時のものであり、現況と異なる場合があります。
ゴルフ用品の一大生産拠点である中国の工場現場から、キャディバッグが出来るまでについてお伝えしています。今回は広東省深セン市にある景恒運動用品(深セン)有限公司を訪れました。
▼前回の記事はこちら
[surfing_other_article id=50567]
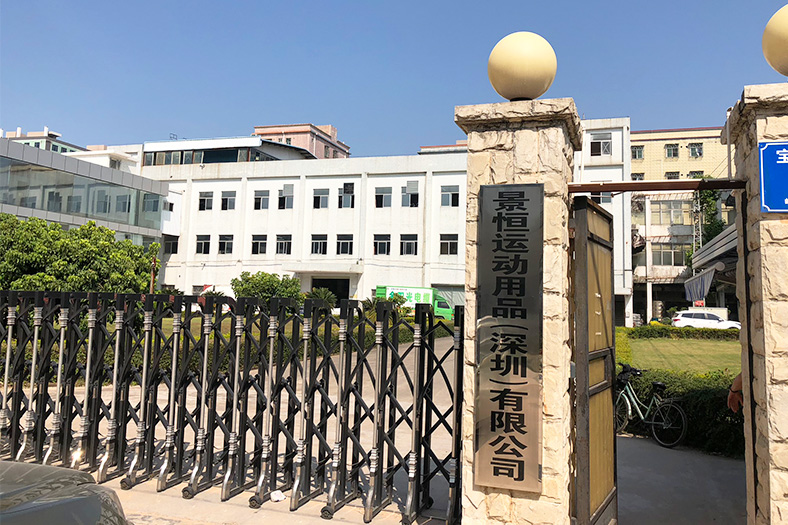
この工場では月産1万2000本程の生産キャパがあり、すぐ隣の系列工場と合わせて月産3万本のキャディバッグを製造しているそうです。
社長の周さんによると、日本の大手メーカーのバッグも製造しているとのこと。シェアは「販売トップ10製品中、6製品位はウチで製造しているよ」と。
具体的なメーカー名・ブランド名は秘密でしたが、「ウチでは材料を生地市場で買ってくることはまずないね。生地メーカーに直接オーダーだよ。品質優先だよ」とのことで、長年の実績を積み上げた信頼の工場でした。
では製造工程を追っていきましょう。
⑥ボンディング
キャディバッグの表面の生地は裏側にスポンジ状の裏地などを接着する「ボンディング」という工程を経た生地を使っています。
キャディバッグのデザインに応じて弾力感や膨らみ具合、耐久性などから、各メーカーは独自の裏地のボンディングを行っていて、そこにはメーカーの哲学も反映されます。コスト優先か、数年後の耐久性か、デザイン性重視か、などです。
表面の生地がメーカーから納品された後、ボンディング加工専門工場に外注し、裏地を貼り合わせます。
⑦生地の裁断
キャディバッグの生地はメーカーからは幅52インチ(約132cm)のロール状に巻かれて納品されていました。ロールは細いものでは直径20㎝位、太いものでは50㎝位になります。これを専用の裁断機にセットします。まずは直線裁断し、長方形にカットしていきます。
次にカットされた生地を4~8枚程重ねて、一度に「型抜き」の要領で裁断していきます。
その工程では金型を使います。金型は片側が切断刃になった幅5cm程度の金属バーを型抜きのように曲げた形で「わっぱ飯」のわっぱのような形をしています。
それを重ねた生地の上に置き、上から油圧プレスして一気に「型抜き」します。裁断機は大型のもので幅2.5m、奥行も1.5m程あり、キャディバッグのサイド部の大きな生地も余裕で「型抜き」出来ます。価格は新品で10万元(170万円)程とのことでした。
⑧刺繍と縫製
次にキャディバッグでデザイン上重要な刺繍をします。デザイン画を表現する「アップリケ刺繍」、ロゴ部の周辺のみ刺繍する「かがり刺繍」、大きな面積を刺繍で表現する「たたみ刺繍」など、どう使うかはデザインの腕の見せ所。各モデルとも工夫をこらしていました。
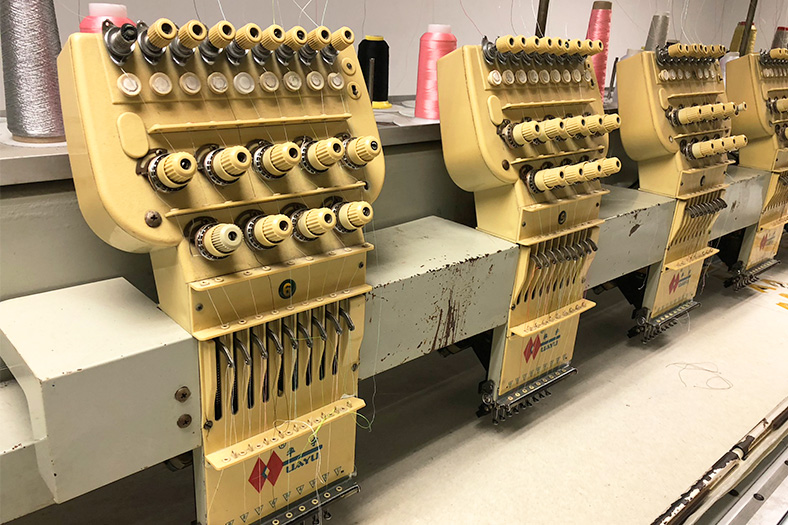
刺繍の工程は切断した生地を電子制御で精密に動くテーブルに10~20枚キレイに並べておき、スタートすると生地1枚につき1本の刺繍針を上から降ろしてゆきます。そして、1秒間に8~10針の超高速で刺繍。小さいロゴなら1分以内で刺繍してしまいます。
次にチャック、ポケットなどをミシンで縫製します。また「パイピング」という細いチューブを生地の境界に取り付け、複数の生地で立体的にしてゆきます。またポケット部も縫製します。
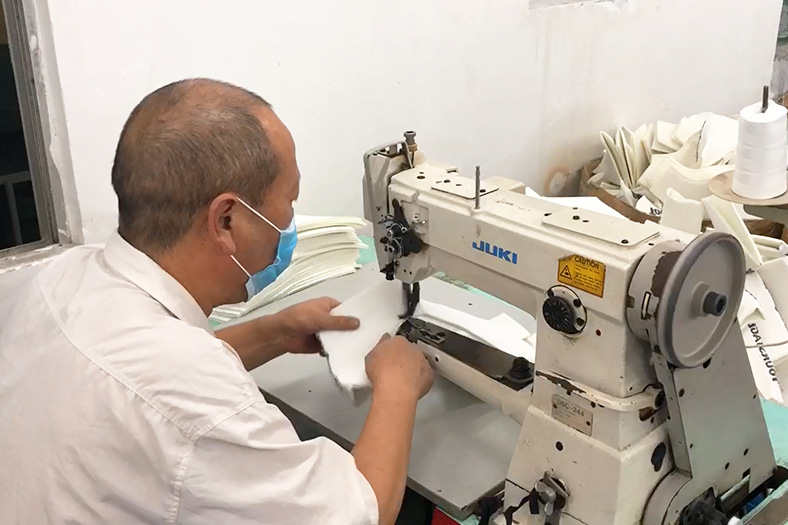
これらの作業はミシンを使った完全な手作業。曲線を多用するキャディバッグは単に工業用ミシンを使える、というスキルでは太刀打ち出来ません。特に大きなサイド部の縫製は、キレイに仕上げるには作業経験が必要で、「シワひとつも絶対に許されない作業だよ」と教えてくれました。
⑨樹脂成形パーツ取付け
最近ではキャディバッグのサイド部はメーカーロゴなどがあり、立体的な造形をしています。これは別にEVA樹脂で成型したパーツを使い、生地の裏側に配置し、生地と高周波で融着して一体化。
周辺はかがり刺繍などをして仕上げます。こうして仕上げた各パーツは最終的に、一つの筒のように縫製されて、キャディバッグの形になっていきます。
⑩骨格となるベルポーレン
まだ、生地を縫い合わせただけなので柔らかい状態です。そこでキャディバッグとしての骨組みを造ります。バッグの中に入っている樹脂製の筒で、ベルポーレンといいます。
厚さ1.4~1.6mm程度の硬い発砲ポリエチレン製の平板をキャディバッグ高さに合わせて長方形に切断。これを筒状に丸め、ホチキスで仮止めします。景恒運動用品では軽量タイプも製造していて、近年人気だそうです。
⑪ボトム、口枠の取付け
次に筒状のベルポーレンに縫製したバッグ生地を被せ、同時にキャディバッグの底の樹脂パーツ(ボトム)を工業用ミシンで太い糸を使ってバッグ生地と一緒に縫い付けます。キャディバッグの下部を見ると、太い糸でハチマキのように縫い付けてある部分です。
次に口枠部も取り付けます。口枠も樹脂一体成型で別工場から納品され、キャディバッグ工場でメッシュ生地を取り付けていきます。これを、縫製とリベットで取り付けていきます。
シャフトが直接当たる箇所ですので、リベットが飛び出ていたりしたら完全にアウトだそうです。また持ち手(ハンドル)、ショルダーベルト金具もリベットで固定していきます。
⑫組立・検査・出荷
最後にショルダーベルト、フードなどを取り付け最終検査。少しでも糸のほつれ、縫製ラインの曲がり、汚れなどがあれば即NG。厳しい品質検査を経て出荷となります。
次回はハンドル、ボトムといった細かいパーツやヘッドカバーの製造現場のレポートをします。どうぞお楽しみに。