月刊ゴルフ用品界2018年2月号に掲載された「現場放浪記 第9回」をWeb用にアップしたものです。なお、記事内容は本誌掲載時のものであり、現況と異なる場合があります。
前回の記事はこちら
[surfing_other_article id=51579]
ゴルフ用品の一大生産拠点である中国の工場現場から、キャディバッグが出来るまでについてお伝えしています。今回はキャディバッグに必要不可欠な金属製パーツの製造現場を訪れました。
五つの金
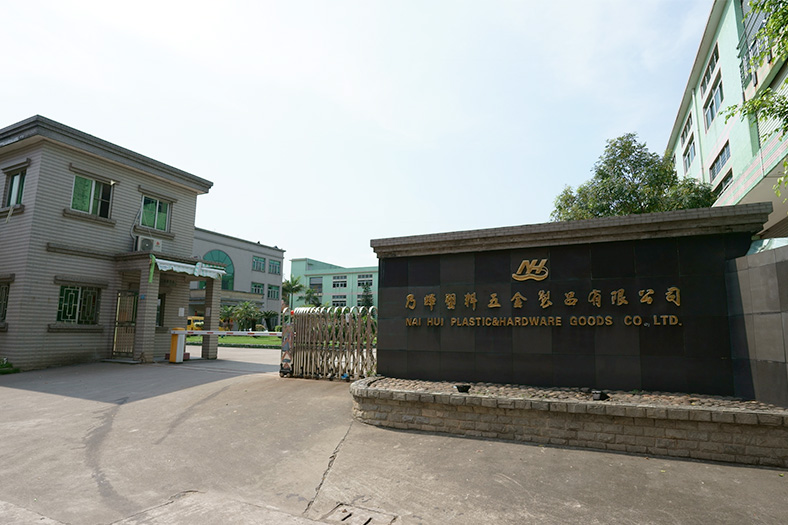
中国の工場地帯である広東省を車で走っていると「〇〇制品五金廠」とある看板をよく見かけます。五金とは元々は「金」「銀」「銅」「鉄」「錫(すず)」を表す言葉ですが、現代では大まかに「金物」を意味し、身近な生活用品に使われる部品を指す言葉になっているようです。
例えば衣類のファスナー金具、ホック、バッグなどの金物、ショルダーベルトの金具など、全て「五金」の工場で製造されています。
キャディバッグではハンドルやショルダーベルトの金具(Dカン、ナスカン)やフードのホック、リベット、銘板、ファスナー引き手が該当します。
今回、広東省東莞市温塘鎮にある東莞乃輝塑料五金制品有限公司を訪れました。ここでは主にファスナー引き手やショルダーベルト金具と、フードを留めるホックを製造しています。創業は1975年。中国に工場を構えて20年で、従業員は現在150名との事でした。
代表部品として、ショルダーベルト部分の金具について順を追ってレポートします。
ダイカスト製法
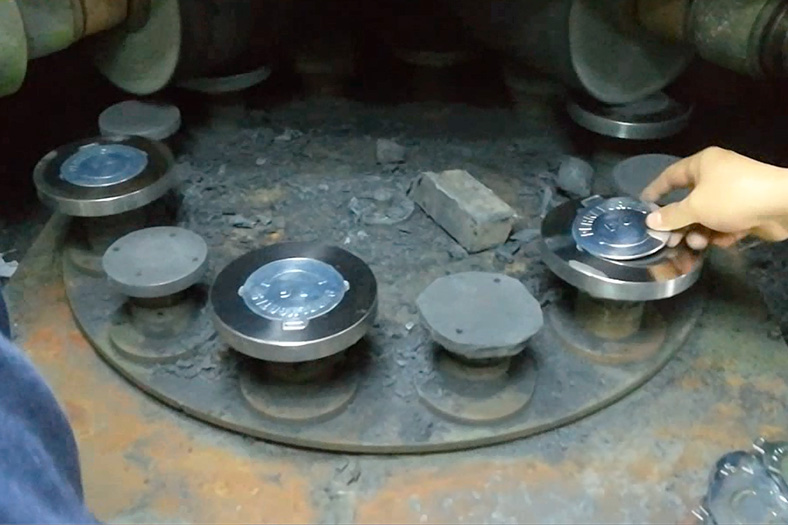
金具の原材料は俗に「ジンク」と呼ばれています。正確には亜鉛合金を指し、亜鉛のほかアルミ、銅、マグネシウムを含有しています。
ダイカスト製法とは、金型に溶けた亜鉛合金を高速で圧入し鋳造する方法です。金型は二つに分かれており、一方が固定され、もう一方が可動式になっています。
ダイカストマシンはこれら2つの金型を油圧で自動的にはめ合わせ、圧力をかけて密着したうえで溶融した亜鉛合金を流し込み鋳造します。冷却後の金型の分解、製品の取り出しまで全自動で行っていました。
社長の林さんによると「この機械1台で1日当たり2千個以上製造できるよ」とのこと。「新品ならこの機械は1台15万元(260万円)するかな」――。この装置が金具工場のキモ。工場では5台ほどのマシンがフル稼働していました。
鋳造された部品はまるで「プラモデル」のように4個~20個程度同じ部品が繋がっていて、次々に出てきます。
カット・バリ取り
次にこれを一つ一つの部品にするため湯口・湯道をカットします。大きな部品では専用金型を使ってプレス抜きをする場合もありますが、小物の場合は手作業で行います。
次に「パーテリングライン」という金型の合わせ目に出来た鋳バリを手作業で除去していきます。作業はプラモデルのバリ取りと全く一緒です。工場ではこの工程で8人の作業員が作業していました。
研磨は半自動化されていた
次は研磨工程です。耐水ペーパーでの自動研磨や回転研磨機を使っての研磨を行っていきます。同じ部品を10個から20個まとめて冶具の上に並べ、研磨機にセットして表面を整え、平滑にします。
また鋳造肌を整える目的や光沢を出す目的でバレル研磨を行います。ヘッドと比べ比較的小さな(直径1.5m程度)振動バレル機に部品と石ころのような研磨剤を入れ、グルグルと回します。この他に水平式の回転バレル機も使い、毎分50回転程度の速度でグルグル回していました。
メッキ工程が美観を決める
亜鉛合金の金具は比較的メッキがしやすいのですが、社長の林さんによると「この成否で品質が決まるから気は抜けない」とのこと。
まずは銅メッキを行います。部品をまとめてカゴに入れ、70cm×50cm程度のメッキ槽にドブ漬けして湿式メッキします。水洗後、仕上げとしてニッケルクロムメッキを行います。こちらもドブ漬けしていますが、電気メッキです。また比較的大きな製品や高級品で金メッキをする場合は、カゴに部品を放り込むのではなく、一つ一つ専用の「吊り金具」にぶら下げてメッキ槽に浸けていきます。
メッキ後水洗し、水分除去。まるで洗濯機の脱水槽のような装置に部品を入れて、遠心力で脱水します。最後に乾燥と脱脂をすれば金具の完成です。
厳しい品質検査
乃輝五金制品廠ではキャディバッグ以外にも多くのバッグ用金具を製造しているため、品質管理も重要。社内検査の項目は、
引張り強度検査
金具が所定の強度を発揮するか。弱いとショルダーベルトが外れて怪我をすることもあるので重要。
メッキ剥離試験
いわゆる碁盤の目試験。メッキの密着性を検査する。テープを貼って剥がしを2回連続し、剥離がないか確認。
メッキ強度テスト
回転バレル機に15分入れて強度試験。不良品では割れたようにメッキが剥離してしまう。
硝酸腐食試験
硝酸試薬を数滴滴下し、30秒酸化に耐えられるか。
塩水耐食試験
5%の食塩水を試験装置内で噴霧し、数日間の経過を観察し腐食の有無を検査。メッキが乗っていない箇所の有無を確認。
こうして製造ロットごとに試験サンプルを抜き取り検査し、記録をしているそうです。林さん曰く「ここまでしてもし1個でも不良が出たらオシマイだよ。単価も安いから儲かってないよ!」との弁。笑顔の裏には品質に対する自信が見え隠れしているようでした。